In this article, Camila Rodríguez and Elisa Díaz, MSSA Conservators, describe the main challenges of Frank Stella’s work treatment, carried out within the framework of the Stella Project
To think about the conservation of modern and contemporary artworks is always a challenge as it involves reflecting on work methodologies which are highly complex as a result of the diversity of materials and techniques -increasingly less conventional- used by artists, which translates into works whose materiality, form and content are communicators of a message. This context push conservators to open up to different material and dialectical needs artists may have, to enter into a dialogue with them that aims to understand the challenges posed by their works.
The main goal of the Stella Project was to design and construct a new stretcher for the large-format work Isfahan III by American artist Frank Stella, since its original one was lost after the 1973 coup d’état and the two former stretchers it had since its recovery in the 90s, did not meet the dimensions of the original and were deficient in structural terms. On the one hand, they were heavy and unstable; on the other, they did not meet the size or depth of Stella’s original stretchers.
This project -developed jointly with Josefina López, Painting Conservator, Director and Consultant of Conservarts- has focused on the search for an appropriate treatment, according to the nature of this work. The particularity of this painting and what makes it complex, in terms of structural conservation, is its large size (304 x 610 cm) and its irregular shape, curved in several areas. Therefore, together with the design of the new stretcher, various technical strategies had to be devised to locate the distribution of tensions in the canvas, elucidate the structural areas where greater force is exerted, and know the physical behavior of the canvas on this irregular shape, in order to resolve the deficiencies of the previous versions of its supporting stretcher.
In order to achieve the above, the participation of an interdisciplinary group of professionals who contributed in an active dialogue from their different expertise was essential to successfully complete this project and the challenges that arose from it. Among them were scientific-chemical conservators, conservators specialized in painting and textiles, artists, wood assembly specialists, art historians, engineers and architects.
- See more about the group of professionals in this link
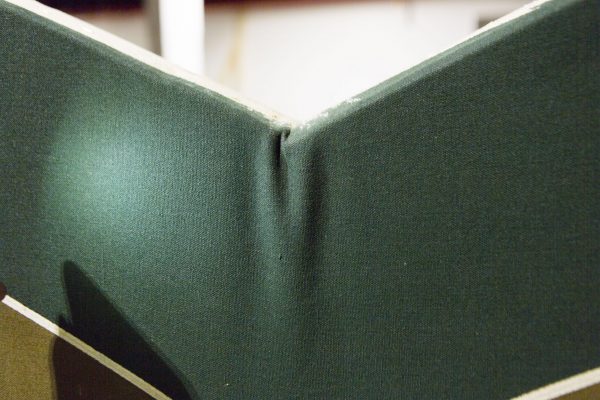
Canvas deformation at the center area before restoration. Imagen: Archivo MSSA. Crédito fotográfico: Josefina López O. © [1968] Frank Stella / Artists Rights Society (ARS), New York
Innovation for the future
The canvas tension studies were developed by the principal project advisor, Antonio Iaccarino Idelson, painting conservator, specialist in stretchers and tension systems, who worked together with Italian engineer Luca Fattore, to be able to clarify by means of the Finite Element Analysis (FEA), a digital simulation, the different states of the continuous tension system needed for Isfahan III. This considered the realization of a digital mapping with precise measurements to detect critical areas and points of stress, allowing to formulate possible solutions for an adequate tensioning of the painting.
The new strainer, built during the development of this project, meets both the technical and formal goals set by the Stella Project team of professionals: to be lighter than the previous one, structurally more rigid and stable, and detachable in four parts just like the original was (which will allow future itinerancy of the work). It also sought to recover the original size and depth of the piece -three inches- which responds to the concept of pictorial construction that the artist had been developing in other series of the 1960s. For Stella, the stretcher is not just a functional structure which supports the canvas, but becomes part of the aesthetic composition of the work, since it visually detaches the painting from the wall and gives it a volumetric character.
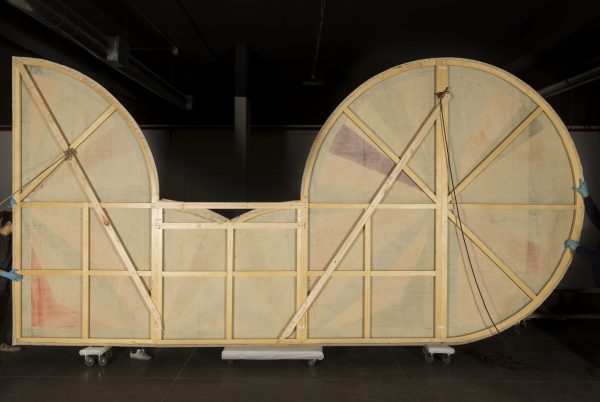
Back view of Isfahan III with its former stretcher. Imagen: Archivo MSSA. Crédito fotográfico: Josefina López O. © [1968] Frank Stella / Artists Rights Society (ARS), New York
To meet these needs, a strainer was designed, its construction was carried out using CNC router cutting technology and its materiality consisted of layers of plywood on the outside and balsa wood with extracted areas on the inside, to structure and reduce its weight. Its design distributes the forces evenly and reinforces the critical stress points that the previous frames had. The four frame sections are joined together by rigid but lightweight carbon fiber plates. Also, removable polycarbonate backs were added to avoid contaminating agents and decrease the vibration of the canvas.
Prior to the construction of the new frame, scientific analyses were carried out on the Isfahan III pictorial layer to determine the composition of the materials used and their adhesion to the canvas. A superficial cleaning of the back of the support and treatments located mainly by the contour were also carried out: removal of old patches and consolidation of weakened fibers and holes produced by staples and/or tacks.
Another decision made by the project’s conservation team was to apply the elastic tension system to the canvas, an innovative procedure that allows it to be mounted by means of elastic tensioners, freeing it from a rigid fastening to the strainer and thus allowing its free accommodation to climatic changes without stressing or producing unnecessary strain. This new system avoids deformations in its support, plane loss and cancels the possibility of tears in the canvas due to the application of staples or tacks.
Since December 2019, the work has successfully adapted to its new tension system and is being monitored to visualize its behavior in the face of climatic changes by means of three displacement sensors located at strategic points of the strainer that are connected to a datalogger that records the perceived variations. This allows to quantitatively detect the response sensitivity of the canvas against relative humidity and helps to determine possible tension adjustments in relation to environmental conditions in which the work may be found.